Microbial Fuel Cells (MFCs) are bio-electrochemical systems that exploit the ability of electro-active microorganisms to colonise an electrode, breakdown organic material and donate electrons to the electrode as part of anaerobic respiration (see Figure). MFCs typically comprise an anode electrode and a cathode electrode separated by a cation exchange membrane. The membrane employed in MFCs is usually non-porous and facilitates the transfer of cations whilst maintaining physical separation between the anode and cathode half-cells.
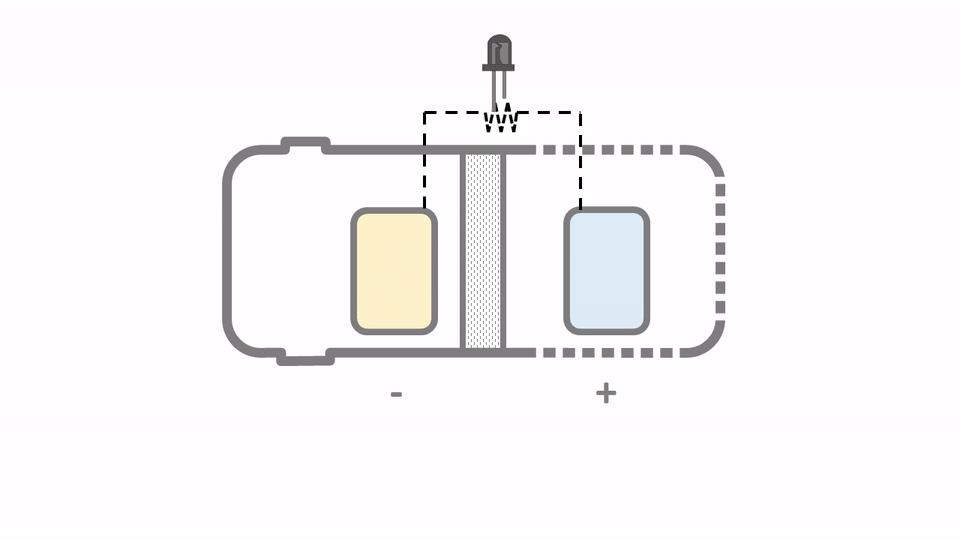
The EVOBLISS project allowed the study of microbial evolution over time, with energy generation as the primary selective pressure. Different types of 3D fabricated substrata will be utilised as MFCs, which will allow the microbial communities to directly transfer electricity on electrodes inside these units. The electricity generated is directly proportional to the rate of growth and metabolism of the microbes, and an essential respiratory pathway.
In other words, the higher the electrical output, the faster the microbes will be growing, and the healthier the microbial community will be. Using electricity as the selective pressure will optimise communities into being more efficient at electron transfer, when fed with different feedstocks. The validation of this line of empirical experiments will ultimately be the inoculation of existing MFCs which are currently being used for powering systems (e.g. EcoBots, pumps, LEDs, mobile phones), to demonstrate the improvement in performance achieved from the evolutionary selected microbial communities.
The MFC make-up
Material properties are critical at ensuring that maximum growth conditions are maintained within the MFCs, which will result in maximum power output performance levels. Since the EvoBot platform has the ability to 3D-print and dispose different substrata with precise compositions and topologies the initial investigation was focused on identifying the optimum materials that can favour the MFC power output. On the investigation the ideal substratum properties were taken into account such as favourable porosity and appropriate conductivity. Also the ideal materials needed to be biocompatible, chemically inert, have a long-life and possess a good structural integrity.
For this initial task the material tested were ceramic, agar, gelatine, alginate, nafion, PLA, ABS and Nanocure®. The results obtained from this experiment regarding ceramic build MFCs using soft materials anode substratum were presented in European Fuel Cell Conference, 2015 and then published in the International Journal of Hydrogen Energy (Ieropoulos et al. 2017). It was concluded that gelatin’s outperformance over the other soft materials, and also its viscous characteristics make it a suitable material to be employed into the 3D process, as a step towards monolithically fabricated MFCs, which can provide nutrients during a starving period or act as an endogenous store of fuel. The material employed in the 3D process can be any soft material, which can be easily extruded using EvoBot and can also be used as a structural material. Apart from that other materials were tested as monolithically printed MFCs made out of sludge anodes in carbon graphite agar (agar conc. 1.5%), having plain agar (conc. 5%) as membrane and FeCN mixed with carbon graphite agar (conc. 2%) as the cathode.
In summary, through this task we identified the different properties of the material required to develop MFC technology in terms of maximising power production from the MFC and in terms of integration with the EvoBot robotic platform.
Interface with EvoBot
The aim of this task was to establish the infrastructure of interconnections in terms of anode (bacterial) and cathode (abiotic) electrodes connection, for real time output capture and recording. This was achieved by connecting the MFCs to a data logger that was controlled via Python and LabView such that individual and collective (stack) MFC readings were able to be recorded. These “plug and play” electrical connections interfaced with the EvoBot controller, for real time feedback loop control. Based on the feedback mechanism the electrical signal of the MFCs under a specified threshold triggered the pumps to dispense the feedstock into the specified beakers and then the syringe to feed the underperforming MFC. The evolutionary changes within the microcosms inside the MFCs were reflected by the increase in voltage output as a result of the feeding and constant maintenance at a certain level. In summary the threshold readings modified based on the user’s needs improved the electrical output of the MFCs by controlling the pumping mechanism of the robotic head to actuate and deliver more fuel when the MFCs were starved (Figure 3.3.1). This is demonstrated nicely in Figure 3.3.2 were by increasing the threshold every day the MFCs were maintained above that level having consistent output.
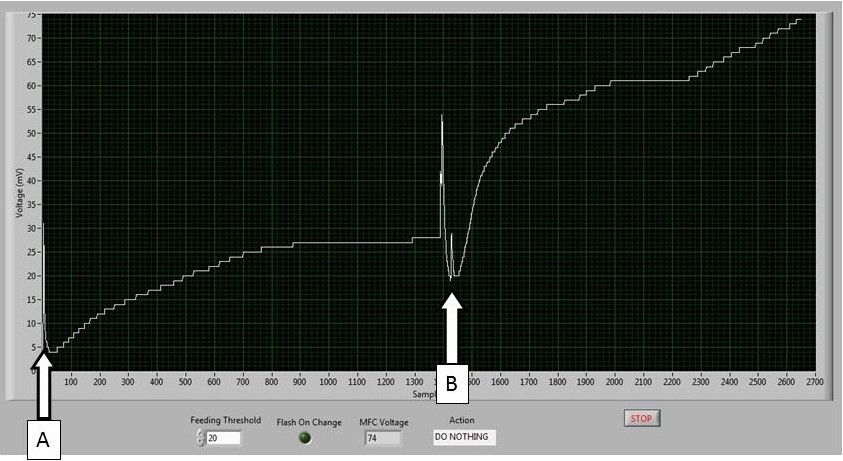
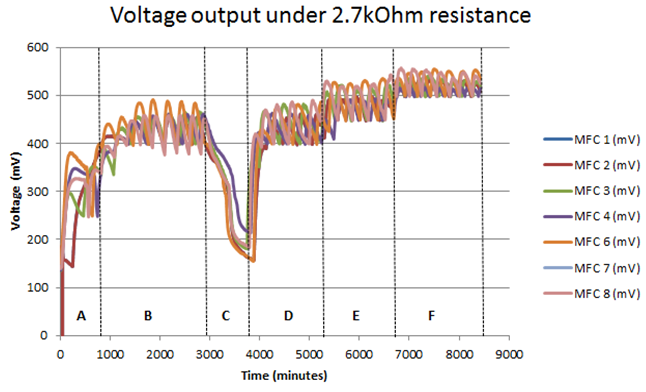
MFC performance optimization
One of the initial focuses of this project was the optimisation of critical MFC components that can make-up an MFC. Since EvoBot gives us the ability to 3D-print, the investigation was focused on 3D-printable materials that can emerge from the EvoBot platform without any further processing. Initially the focus was on the material that can act as the ion exchange membrane of the MFC and the physical separator between the anode and the cathode. Through these experimentations novel printable/ extrude-able materials that were proven favourable to the microbial community were identified such as kilned terracotta, air-dry terracotta clay and air-dry white modelling clay (Fimo™). The ability of these materials to act as viable separators was tested against the commercially available and widely used cation exchange membrane (CEM). In summary, that bench experiment demonstrated that soft materials that cure in air can be used as membranes for the MFCs and can improve the power output as they offer a great advantage over the conventional and expensive cation exchange membranes, which is a novelty in the MFC field. Since the EvoBot platform is flexible and can be modified accordingly to extrude such membranes; this has been considered a step towards 3D printable MFCs. In addition, the replacing of carbon veil electrodes to the conductive paste, is a valuable development towards printable MFCs as both the membrane and the cathode electrodes can emerge from the same source (Figure 3.3.3). These results have been presented in the European Fuel Cell Conference, 2017 and were published in the Book of proceedings (Theodosiou, Greenman, et al. 2017).
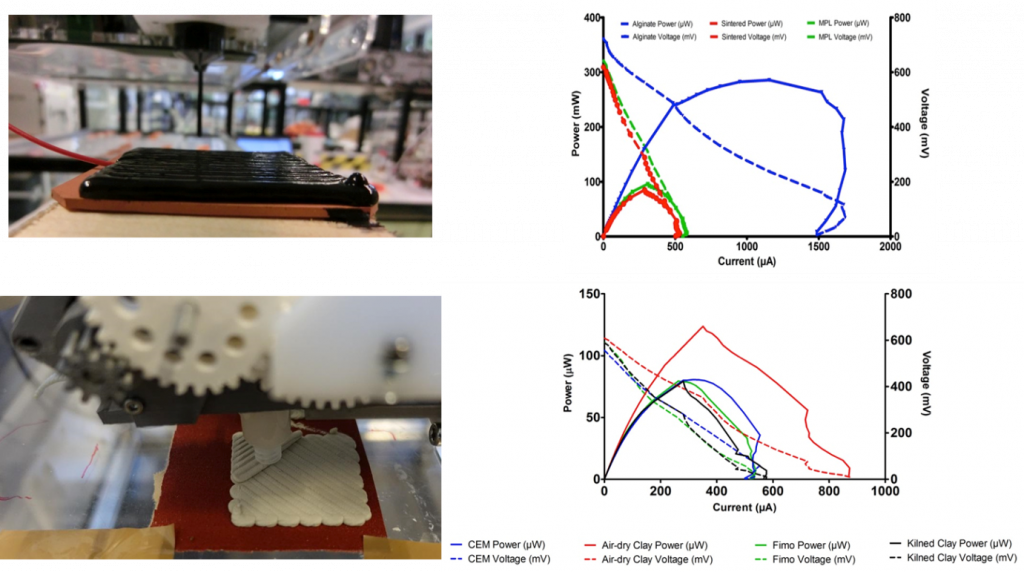
The aforementioned experiments were focused on the optimisation of critical MFC components, but at the same time we were investigating the selective pressures that would affect the microbial community, such as pH and medium salinity and therefore affect the power production. A significant selective pressure is the type and mixture of carbon energy sources that are required by the community to grow and survive. The initial experiments provided us with the preliminary data about different substrates which can, and cannot be utilised by the microbial communities within the anodic reactors. These insights inspired and were then used, to optimising substrate combinations for general MFC experiments through EvoBot algorithmic evolutionary experiments. That experiment employed five different seed sources were used from a variety of different geographical locations (activated sludge, port sediment, river sediment, ochre soil and slurry). The results highlighted the ubiquity of microbial communities from a wide range of environmental habitats to metabolise different single carbon energy sources. The data that has been generated regarding the different substrates which can and cannot be utilised were deployed within the Evobliss project for optimising substrate combinations.
Environmental condition optimization
This task focused on the investigation and optimisation of the environmental parameters for faster growth and maximum power transfer in microbial fuel cells (MFCs). Two experiments were performed under this task. In this experiment EvoBot was tested as a platform of maintaining microbial fuel cells (MFCs) by feeding them incremental concentrations of organic substrates based on the feedback loop mechanism described above. As a result of this interaction, the MFC continued to perform and the experiment was prolonged. The feedstock tested were acetate, lactate and cellulose at incremental concentrations of 0,25%, 0.5% and 1%. The experiment succeeded in showcasing that EvoBot successfully operated long term interactive microbial fuel cell experiments and optimised the substrate concentration of the media in response to the MFC power output profile and at the same time gave us valuable empirical understanding of the EvoBot changes that needed to be done for future use. More details of this experiment are published in Theodosiou et al. 2017.
The second experiment resulted in accomplishing one of the envisaged goals of Evobliss which was the first pioneering attempt at functionalising the 3D printing technology by combining it with the chemostat methods. The chemostat mimicking experiment (Theodosiou, Faina, et al. 2017) received the award of Best Biology Paper in Living Machines conference that took place in Stanford University, July 2017.
Anodophilic motility through conductive wet channels
The aim of Task 4.5 was to experiment with an adventurous approach of inoculating a single microbial fuel cell (MFC) and allow motile microorganisms to perform ‘taxis’ to inoculate and colonize the downstream sterile MFCs. The experiment described below is a successful demonstration of upstream and downstream microbial expansion from one MFC unit to another. Even though in the original proposal the means of verification were going to be video or photographic, it was actually possible to demonstrate the microbial expansion through the recording of power increase from the un-inoculated MFCs; these data have higher scientific impact. In summary, the experiment consisted of a cascade of six MFCs which were connected fluidically in series (i.e. each anode was connected via tube to the next anode). Only a single ‘parent’ MFC was inoculated with activated sludge (positioned in the middle of the cascade). The cascade system was fed continuously with perfusion media which was pumped through the first MFC and then flowed through the cascade before exiting the system. In summary, it was demonstrated that anodophilic microorganisms were able to both down- and up-inoculate (migrate and expand) through an MFC cascade and begin to generate power in MFCs that otherwise sterile. In addition, the novel use of community level physiological profiling (CLPP) identified many similarities (and dissimilarities) between MFCs and the utilisation of specific carbon energy substrates by the anode biofilm. These different types of feedstock can be used as ‘target substrates’, by the EvoBot platform and optimise the power output of diverse MFC units.
EcoBot evaluation
EvoBot evolved MFCs were unplugged from the EVOBOT platform and formed the Microbial Fuel Cell power pack of EcoBot-II, these MFCs demonstrated improved performance levels as a result of the EvoBot nurturing process. EcoBot operates on a pulsated-motion-behavior, which means that there are periods of idleness when energy is being accumulated. The length of time it takes for a particular energy level to be reached is defined by the electrical performance of the on-board MFCs. Thus, if the MFC performance has improved as a result of the EVOBLISS evolutionary process, then this will be directly reflected in EcoBot’s behavioral repertoire and ability to actuate more frequently, resulting in a more dynamic behaviour. The normal procedure for maturing a microbial consortium for optimum energy production inside MFCs, usually takes longer than 4 weeks and depending on the environmental conditions, this can continue for up to 3 months. Using the EvoBot we demonstrated that MFCs inoculated and maintained for just 6 days can power Ecobot-II and decrease the idleness to as low as 1 minute. This allowed the Ecobot-II to cover 20 cm length in less than 14 minutes whereas its precursors needed 5.2 hours.
In summary, it was successfully demonstrated that the EVOBLISS project created a robotic machine than can accelerate the maturing produce of MFC-compatible energy-producing cultures at a much shorter period of time. This shows that EvoBot is the first of its kind to enforce, monitor and interact with evolving systems for producing optimally evolved/adapted systems designed for specific tasks; in this particular instance, the microbial element was evolved to efficient energy generation suitable for powering a low-power robot such as Ecobot-II.
References
Faíña, A. et al., 2016. EvoBot : An Open-Source , Modular Liquid Handling Robot for Nurturing Microbial Fuel Cells. In Proceedings of the Artificial Life Conference 2016. pp. 626–633.
Ieropoulos, I. et al., 2017. Gelatin as a promising printable feedstock for microbial fuel cells (MFC). International Journal of Hydrogen Energy, 42(3), pp.1783–1790. Available at: http://dx.doi.org/10.1016/j.ijhydene.2016.11.083.
Theodosiou, P., Faina, A., et al., 2017. EvoBot: Towards a Robot-Chemostat for Culturing and Maintaining Microbial Fuel Cells (MFCs). In Biomimetic and Biohybrid Systems. Springer, Cham, pp. 453–464. Available at: http://link.springer.com/10.1007/978-3-319-63537-8_38 [Accessed October 12, 2017].
Theodosiou, P., Greenman, J., et al., 2017. Towards monolithically printed mfcs: a report on the development of a 3d-printable membrane electrode assembly (mea). In European Fuel Cell Technology & Applications Conference -Piero Luighi Conference. pp. 279–280.